Cooling Workshop of Your Food Factory Can Do Like This
Views: 89 Update date: Jul 05,2025
Cooling Workshop of Your Food Factory Can Do Like This
The Two-Stage Cooling Strategy
Stage 2: Traditional Cooling Room (Core Temperature Control)
Focuses refrigerated energy on core cooling (e.g., 60°C → 4°C in ≤90 mins per FDA).
Smaller size/lower load cuts energy use 25–40%.
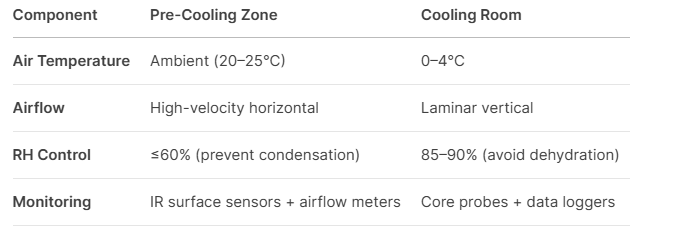
Why This Works: Science & Compliance
Pathogen Control:
Pre-cooling rapidly exits the "danger zone" (60°C→21°C in ≤2 hrs), stifling bacterial growth.
Prevents condensation (a biofilm risk) in cold rooms.
Cooling processes must minimize microbial growth."
Product Quality:
Avoids "case hardening" in baked goods (crust seals in steam).
Reduces ice crystals in meats/fried foods.
Energy Efficiency:
Removing 70% of heat via airflow slashes refrigeration costs.
Smaller cold room = lower compressor load.
Implementation Checklist
Zoning: Physically separate pre-cooling and cooling areas with positive air pressure toward pre-cooling.
Equipment:
Pre-Cooling: Axial exhaust fans + HEPA-supplied air.
Cooling: Blast chillers with defrost cycles.
Validation:
Map surface/core temps using data loggers.
Swab pre-cooling exhaust ducts quarterly for microbial buildup.
Case Example: Soup Manufacturer
Problem: Cooling 90°C soup in a single stage caused inconsistent core temps (4–12°C) and mold in pipes.
Solution:
Added 15m pre-cooling tunnel with exhaust hoods.
Result: Core temp stabilized at 4±0.5°C, 30% faster throughput, zero condensation in chillers.
Conclusion: Smarter Cooling, Stronger Compliance
A purpose-built pre-cooling zone isn’t just engineering – it’s your shield against safety failures and energy waste.
Prev: Choosing a Boot Washer: Why Automation Wins Every Time
Next: The Birth of the Access Control and Cleaning Disinfection Integrated Machine: Hand Washing + Drying + Disinfection + Shoe Cleaning + Access Door
Introduction: The Hidden Risk in Rapid Cooling
Rushing hot food directly into cold rooms creates thermal shock – trapping surface heat while struggling to lower core temperatures. This
imbalance risks microbial growth, texture damage, and energy waste. A smarter approach? Implement a dedicated pre-cooling zone before
final chilling. Here's how to design it for BRC compliance and peak performance.
The Two-Stage Cooling Strategy
Stage 1: Pre-Cooling Workshop (Surface Heat Removal)
Purpose
- Strip surface heat using controlled airflow, not refrigeration.
- Air Supply/Exhaust System: Position supply vents below product lines and exhaust vents above to capture rising hot air (chimney effect).
- Air Velocity: 1.5–2.5 m/sec across product surfaces (adjust for density).
- Ambient Air: Use filtered room air (20–25°C) – no chilled air needed.
- Target: Reduce surface temp to ≤35°C before cold-stage entry.
Stage 2: Traditional Cooling Room (Core Temperature Control)
Focuses refrigerated energy on core cooling (e.g., 60°C → 4°C in ≤90 mins per FDA).
Smaller size/lower load cuts energy use 25–40%.
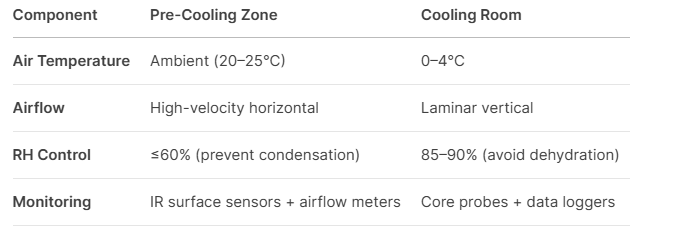
Why This Works: Science & Compliance
Pathogen Control:
Pre-cooling rapidly exits the "danger zone" (60°C→21°C in ≤2 hrs), stifling bacterial growth.
Prevents condensation (a biofilm risk) in cold rooms.
Cooling processes must minimize microbial growth."
Product Quality:
Avoids "case hardening" in baked goods (crust seals in steam).
Reduces ice crystals in meats/fried foods.
Energy Efficiency:
Removing 70% of heat via airflow slashes refrigeration costs.
Smaller cold room = lower compressor load.
Implementation Checklist
Zoning: Physically separate pre-cooling and cooling areas with positive air pressure toward pre-cooling.
Equipment:
Pre-Cooling: Axial exhaust fans + HEPA-supplied air.
Cooling: Blast chillers with defrost cycles.
Validation:
Map surface/core temps using data loggers.
Swab pre-cooling exhaust ducts quarterly for microbial buildup.
Case Example: Soup Manufacturer
Problem: Cooling 90°C soup in a single stage caused inconsistent core temps (4–12°C) and mold in pipes.
Solution:
Added 15m pre-cooling tunnel with exhaust hoods.
Result: Core temp stabilized at 4±0.5°C, 30% faster throughput, zero condensation in chillers.
Conclusion: Smarter Cooling, Stronger Compliance
A purpose-built pre-cooling zone isn’t just engineering – it’s your shield against safety failures and energy waste.